The Basics of Metal Stamping
Metal stamping is a manufacturing process used to convert flat metal sheets into specific shapes. It is a complex process that can include a number of metal forming techniques — blanking, punching, bending and piercing, to name a few.
There are thousands of companies across the that offer metal stamping services to deliver components for industries in automotive, aerospace, medical, and other markets.As global markets evolve, there is an escalated need for quickly-produced large quantities of complex parts.
The following guide illustrates best practices and formulas commonly employed in the metal stamping design process and includes tips to incorporate cost cutting considerations into parts.
Stamping Basics
Stamping — also called pressing — involves placing flat sheet metal, in either coil or blank form, into a stamping press. In the press, a tool and die surface form the metal into the desired shape. Punching, blanking, bending, coining, embossing, and flanging are all stamping techniques used to shape the metal.
Before the material can be formed, stamping professionals must design the tooling via CAD/CAM engineering technology. These designs must be as precise as possible to ensure each punch and bend maintains proper clearance and, therefore, optimal part quality. A single tool 3D model can contain hundreds of parts, so the design process is often quite complex and time-consuming.
Once the tool’s design is established, a manufacturer can use a variety of machining, grinding, wire EDM and other manufacturing services to complete its production.
Types of Metal Stamping
There are three major types of metal stamping techniques: progressive, fourslide and deep draw.
Progressive Die Stamping
Progressive die stamping features a number of stations, each with a unique function.
First, strip metal is feds through a progressive stamping press. The strip unrolls steadily from a coil and into the die press, where each station in the tool then performs a different cut, punch, or bend. The actions of each successive station add onto the work of the previous stations, resulting in a completed part.
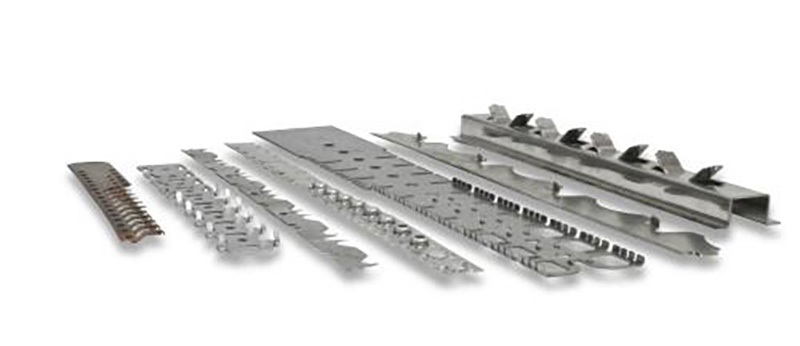
A manufacturer might have to repeatedly change the tool on a single press or occupy a number of presses, each performing one action required for a completed part. Even using multiple presses, secondary machining services were often required to truly complete a part. For that reason, progressive die stamping is the ideal solution for metal parts with complex geometry to meet:
- Faster turnaround
- Lower labor cost
- Shorter run length
- Higher repeatability

Fourslide Stamping
Fourslide, or multi-slide, involves horizontal alignment and four different slides; in other words, four tools are used simultaneously to shape the workpiece. This process allows for intricate cuts and complex bends to develop even the most complex parts.
Fourslide metal stamping can offer several advantages over traditional press stamping that make it an ideal choice for many applications. Some of these advantages include:
1.Versatility for more complex parts
2.More flexibility for design changes
As its name implies, a fourslide has four slides — meaning that up to four different tools, one per slide, can be used to achieve multiple bends simultaneously. As material feeds into a fourslide, it is bent in quick succession by each shaft that is equipped with a tool.
Deep Draw Stamping
Deep drawing involves pulling a sheet metal blank into the die via a punch, forming it into a shape. The method is referred to as “deep drawing” when the depth of the drawn part exceeds its diameter. This type of forming is ideal for creating components that need several series of diameters and is a cost-effective alternative to turning processes, which typically require using up more raw materials. Common applications and products made from deep drawing include:
1.Automotive components
2.Aircraft parts
3.Electronic relays
4.Utensils and cookware
Deep Draw Stamping
Deep drawing involves pulling a sheet metal blank into the die via a punch, forming it into a shape. The method is referred to as “deep drawing” when the depth of the drawn part exceeds its diameter. This type of forming is ideal for creating components that need several series of diameters and is a cost-effective alternative to turning processes, which typically require using up more raw materials. Common applications and products made from deep drawing include:
1.Automotive components
2.Aircraft parts
3.Electronic relays
4.Utensils and cookware
Short Run Stamping
Short run metal stamping requires minimal upfront tooling expenses and can be an ideal solution for prototypes or small projects. After the blank is created, manufacturers use a combination of custom tooling components and die inserts to bend, punch or drill the part. The custom forming operations and smaller run size can result in a higher per-piece charge, but the absence of tooling costs can make short run more cost-efficient for many projects, especially those requiring fast turnaround.
Manufacturing Tools for Stamping
There are several steps in producing metal stamping. The first step is designing and manufacturing the actual tool used to create the product.
Let’s take a look at how this initial tool is created: Stock Strip Layout & Design: A designer uses is used to design the strip and determine dimensions, tolerances, feed direction, scrap minimization and more.
Tool Steel and Die Set Machining: CNC ensures a higher level of precision and repeatability for even the most complex dies. Equipment like 5-axis CNC mills and wire can cut through hardened tool steels with extremely tight tolerances.
Secondary Processing: Heat treating is applied to metal parts to enhance their strength and make them more durable for their application. Grinding is used to finish parts requiring high surface quality and dimension accuracy.
Wire EDM: Wire electrical discharge machining shapes metal materials with an electrically-charged strand of brass wire. Wire EDM can cut the most intricate shapes, including small angles and contours.
Metal Stamping Design Processes
Metal stamping is a complex process that can include a number of metal forming processes —blanking, punching, bending, and piercing and more. Blanking: This process is about cutting the rough outline or shape of the product. This stage is about minimizing and avoiding burrs, which can drive up the cost of your part and extend lead time. The step is where you determine hole diameter, geometry/taper, the spacing between edge-to-hole and insert the first piercing.

Bending: When you are designing the bends into your stamped metal part, it is important to allow for enough material — make sure to design your part and its blank so that there is enough material to perform the bend. Some important factors to remember:
1.If a bend is made too close to the hole, it can become deformed.
2.Notches and tabs, as well as slots, should be designed with widths that are at least 1.5x the thickness of the material. If made any smaller, they can be difficult to create due to the force exerted on punches, causing them to break.
3.Every corner in your blank design should have a radius that is at least half of the material thickness.
4.To minimize instances and severity of burrs, avoid sharp corners and complex cutouts when possible. When such factors cannot be avoided, be sure to note burr direction in your design so they can be taken into account during stamping
Coining: This action is when the edges of a stamped metal part are struck to flatten or break the burr; this can create a much smoother edge in the coined area of the part geometry; this can also add additional strength to localized areas of the part and this can be utilized to avoid secondary process like deburring and grinding. Some important factors to remember:
Plasticity and grain direction – Plasticity is the measure of permanent deformation a material undergoes when subjected to force. Metals with more plasticity are easier to form. Grain direction is important in high strength materials, such as tempered metals and stainless steel. If a bend goes along the grain of a high strength, it can be prone to cracking.
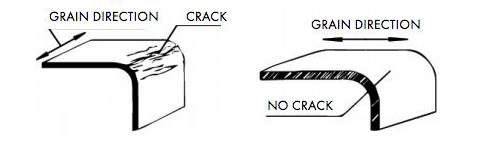
Bend Distortion/Bulge: The bulging caused by bend distortion can be as large as ½ the material thickness. As material thickness increases and bend radius decreases the distortion/bulge becomes more severe. Carrying Web and “Mismatch” Cut: This is when a very slight cut-in or bump-out on the part is required and is typically about .005” deep. This feature is not necessary when utilizing compound or transfer type tooling but is required when utilizing progressive die tooling.
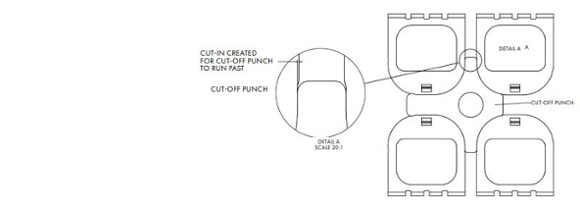
Custom Stamped Part for Vital Monitoring Equipment in the Medical Industry
A client in the medical industry approached MK to custom metal stamp a part that would be used as a spring and electronics shield for vital monitoring equipment in the medical field.
1.They needed a stainless steel box with spring tab features and were having trouble finding a supplier who would provide a high-quality design at an affordable price within a reasonable timeline.
2.To meet the client’s unique request to plate only one end of the part — rather than the entire part — we partnered with an industry-leading tin-plating company that was able to develop an advanced single-edge, selective plating process.
MK was able to meet the complex design requirements using a material stacking technique that allowed us to cut many part blanks at once, limiting costs and reducing lead times.
Stamped Electrical Connector for a Wiring and Cable Application
1.The design was highly complex; these covers were meant to be used as daisy chain cables inside in-floor and under-floor electrical raceways; therefore, this application inherently presented strict size limitations.
2.The manufacturing process was complicated and expensive, as some of the client’s jobs required a fully completed cover and others did not — meaning AFC had been creating the parts in two pieces and welding them together when needed.
3.Working with a sample connector cover and a single tool provided by the client, our team at MK was able to reverse engineer the part and its tool. From here, we designed a new tool, which we could use in our 150-ton Bliss progressive die stamping press.
4.This allowed us to manufacture the part in one piece with interchangeable components, rather than manufacturing two separate pieces as the client had been doing.
This allowed for significant cost savings — 80% off the cost of a 500,000-part order — as well as a lead time of four weeks rather than 10.
Custom Stamping for Automotive Airbags
An automotive client required a high-strength, pressure-resistant metal grommet for use in airbags.
1. With a 34 mm x 18 mm x 8 mm draw, the grommet needed to maintain a tolerance of 0.1 mm, and the manufacturing process needed to accommodate the unique material stretching inherent in the final application.
2. Because of its unique geometry, the grommet could not be produced using transfer press tooling and its deep draw presented a unique challenge.
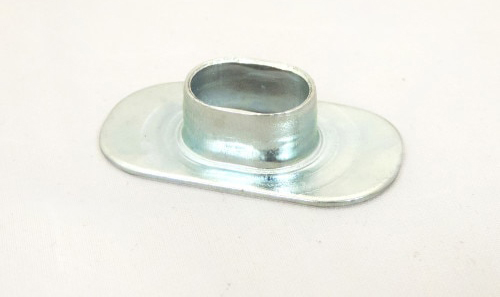
The MK team built a 24-station progressive tool to ensure proper development of the draw and used DDQ steel with zinc plating to ensure optimal strength and corrosion resistance. Metal stamping can be used to create complex parts for a huge range of industries. Curious to learn more about the various custom metal stamping applications we’ve worked on? Visit our Case Studies page, or reach out to the MK team directly to discuss your unique needs with an expert.