What Is Welding?
The weld ability of the metal refers to the adaptability of the metal material to the welding process, mainly refers to the difficulty of obtaining high-quality welded joints under certain welding process conditions. Broadly speaking, the concept of "weld ability" also includes "availability" and "reliability". Weld ability depends on the characteristics of the material and the process conditions used. The weld ability of metal materials is not static but develops for example, for materials that were originally considered to be poor in weld ability, with the development of science and technology, new welding methods have become easier to weld, that is, the weld ability has become better. Therefore, we cannot leave the process conditions to talk about weld ability.
Weld ability includes two aspects: one is the joint performance, that is, the sensitivity of forming welding defects under certain welding process conditions; the second is the practical performance, that is, the adaptability of the welded joint to the use requirements under certain welding process conditions.
Welding Methods
1.Laser welding(LBW)
2.ultrasonic welding (USW)
3.diffusion welding(DFW)
4.etc
1.Welding is a process of joining materials, usually metals, by heating the surfaces to the point of melting and then allowing them to cool and solidify, often with the addition of a filler material. The weldability of a material refers to its ability to be welded under certain process conditions, and depends on both the material's characteristics and the welding process used.
2.Weldability can be divided into two aspects: joint performance and practical performance. Joint performance refers to the sensitivity of forming welding defects under certain welding process conditions, while practical performance refers to the adaptability of the welded joint to the use requirements under certain welding process conditions.
3.There are various welding methods, including laser welding (LBW), ultrasonic welding (USW), and diffusion welding (DFW), among others. The choice of welding method depends on the materials being joined, the thickness of the materials, the required joint strength, and other factors.
What Is Laser Welding?
Laser welding, also known as laser beam welding (“LBW”), is a technique in manufacturing whereby two or more pieces of material (usually metal) are joined together through the use of a laser beam.
It is a non-contact process that requires access to the weld zone from one side of the parts being welded.
The heat created by the laser melts the material on both sides of the joint, and as the molten material mixes and resolidifies, it fuses the parts.
The weld is formed as the intense laser light rapidly heats the material – typically calculated in milliseconds.
The laser beam is a coherent (single-phase) light of a single wavelength (monochromatic). The laser beam has low beam divergence and high energy content that will create heat when it strikes a surface
Like all forms of welding, the details matter when using LBW. You can use different lasers and various LBW processes, and there are times when laser welding is not the best choice.
Laser Welding
There are 3 types of laser welding:
1.Conduction mode
2.Conduction/penetration mode
3.Penetration or keyhole mode
These types of laser welding are grouped by the amount of energy delivered to the metal. Think of these as low, medium, and high energy levels of laser energy.
Conduction Mode
Conduction mode delivers low laser energy to the metal, resulting in low penetration with a shallow weld.
It is good for joints that do not need high strength as the results are a kind of continuous spot weld. Conduction welds are smooth and aesthetically pleasing, and they are typically wider than they are deep.
There are two types of conduction mode LBW:
1.Direct Heating: The part’s surface is heated directly by a laser. Heat is then conducted into the metal, and portions of the base metal melt, fusing the joint when the metal resolidifies.
2.Energy Transmission: A special absorbing ink is first placed at the joint’s interface. This ink takes in the laser’s energy and generates heat. The underlying metal then conducts the heat into a thin layer, which melts, and resolidifies to form a welded joint.
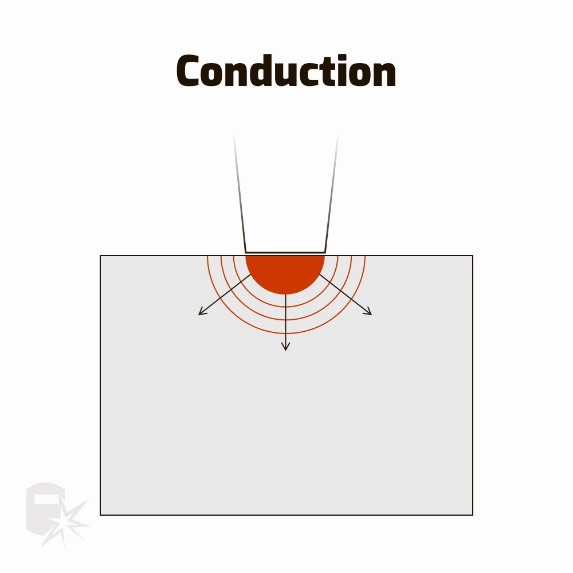
Conduction/Penetration Mode
Some may not acknowledge this as one of the modes. They feel there are only two types; you either conduct heat into the metal or vaporize a small metal channel, allowing the laser down into the metal.
But the conduction/penetration mode uses “medium” energy and results in more penetration. But the laser is not strong enough to vaporize metal like in the keyhole mode.
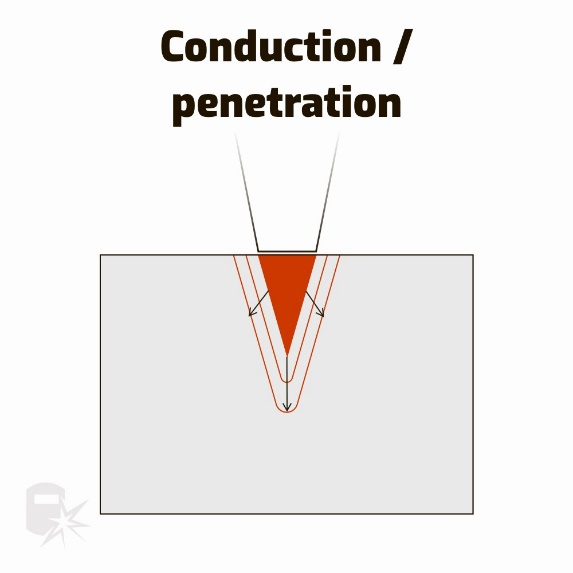
Penetration Or Keyhole Mode
This mode creates deep, narrow welds. So, some call it penetration mode. The welds made are normally deeper than wide and stronger than conduction mode welds.
With this type of LBW welding, a high-powered laser vaporizes the base metal, creating a narrow tunnel known as a “keyhole” that extends down into the joint. This “hole” provides a conduit for the laser to penetrate deep into the metal.
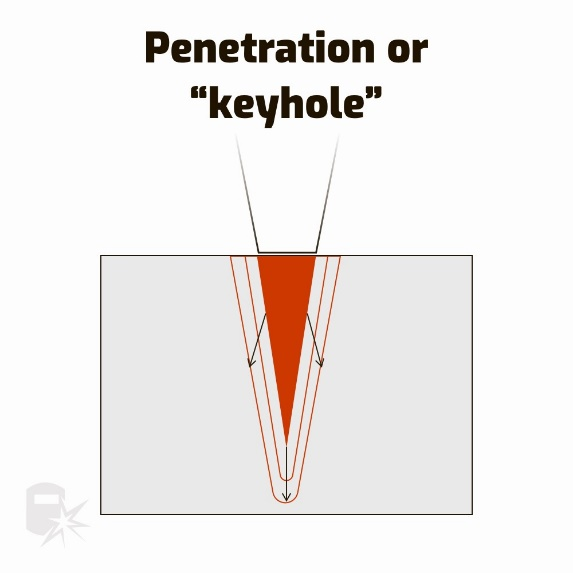
Suitable Metals For LBW
Laser welding works with many metals, like:
- Carbon Steel
- Aluminum
- Titanium
- Low alloy and stainless steel
- Nickel
- Platinum
- Molybdenum
Ultrasonic welding
Ultrasonic welding (USW) is the joining or reforming of thermoplastics through the use of heat generated from high-frequency mechanical motion. It is accomplished by converting high-frequency electrical energy into high-frequency mechanical motion. That mechanical motion, along with applied force, creates frictional heat at the plastic components’ mating surfaces (joint area) so the plastic material melts and forms a molecular bond between the parts.
BASIC PRINCIPLE OF ULTRASONIC WELDING
1.Parts in Fixture: The two thermoplastic parts to be assembled are placed together, one on top of the other, in a supportive nest called a fixture.
2.Ultrasonic Horn Contact: A titanium or aluminum component called a horn is brought into contact with the upper plastic part.
3.Force Applied: A controlled force or pressure is applied to the parts, clamping them together against the fixture.
4.Weld Time: The ultrasonic horn is vibrated vertically 20,000 (20 kHz) or 40,000 (40 kHz) times per second, at distances measured in thousandths of an inch (microns), for a predetermined amount of time called weld time. Through careful part design, this vibratory mechanical energy is directed to limited points of contact between the two parts. The mechanical vibrations are transmitted through the thermoplastic materials to the joint interface to create frictional heat. When the temperature at the joint interface reaches the melting point, plastic melts and flows, and the vibration is stopped. This allows the melted plastic to begin cooling.
5.Hold Time: The clamping force is maintained for a predetermined amount of time to allow the parts to fuse as the melted plastic cools and solidifies. This is known as hold time. (Note: Improved joint strength and hermeticity may be achieved by applying a higher force during the hold time. This is accomplished using dual pressure).
6.Horn Retracts: Once the melted plastic has solidified, the clamping force is removed and the ultrasonic horn is retracted. The two plastic parts are now joined as if molded together and are removed from the fixture as one part.
Diffusion Welding, DFW
Joining process by heat and pressure where the contact surfaces are joined by diffusion of atoms.
The process
Two workpieces [1] at different concentrations are placed between two presses [2]. The presses are unique for each combination of the workpieces, with the result that a new design is required if product design changes.
The heat equivalent to about 50-70% of the materials melting point is then supplied to the system, increasing the mobility of the atoms of the two materials.
The presses are then pressed together, causing the atoms to start diffusing between the materials at the contact area [3]. The diffusion takes place due to the workpieces being of different concentrations, while the heat and pressure only make the process easier. The pressure is therefore used to get the materials contacting surfaces as close as possible so that atoms can more easily diffuse. When the desired proportion of atoms are diffused, the heat and pressure are removed and the bonding processing is completed.
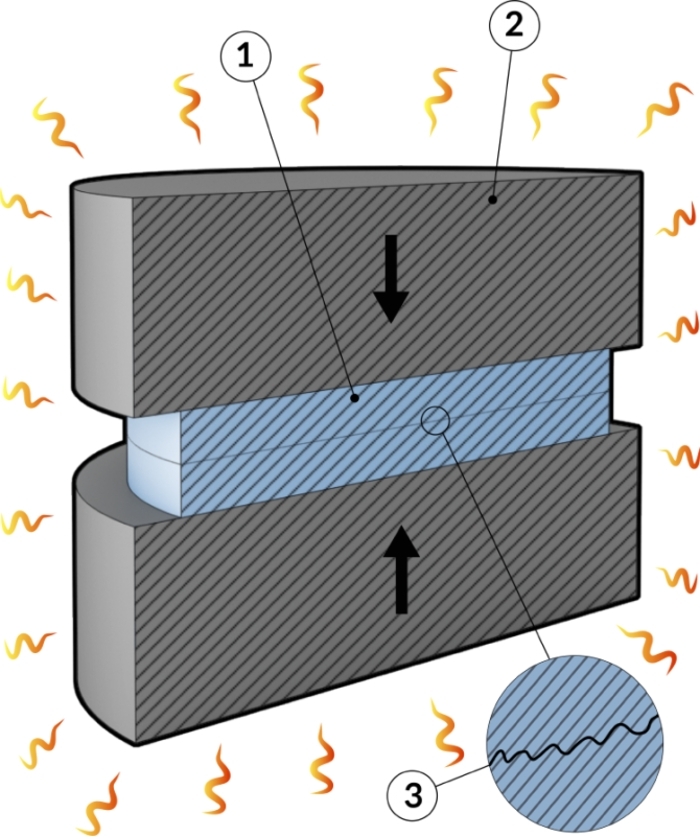